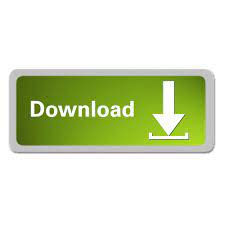
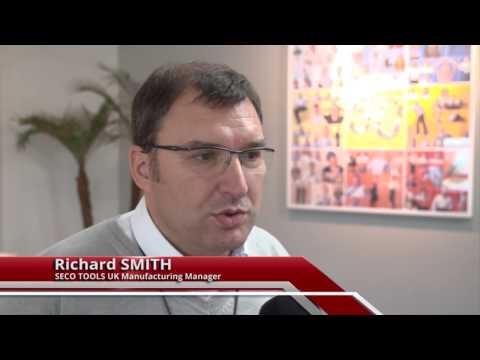


Basically it’ll reduce the nuts and bolts of setting the part up and getting to the toolpath generation much quicker.” “It’ll take out a lot of the mundane operations that we do day to day, such as repeats, rotations, orientating them in the correct way, and setting stock. Andrew Wright, Production Engineer for both Newburgh Engineering and the Nuclear Advanced Manufacturing Research Centre, expects Workflow to reduce part setting up time.“It’ll speed up the programming process, so we can start cutting metal much quicker than in the past.” Waveform is now Aerogrind Tooling’s default roughing strategy, according to Managing Director Tim Shillabeer, who said: “We’ve used it successfully in many recent applications.” And he forecast that Workflow will enable him to provide a better, faster and more efficient service to customers.Tom Newbery, Technical Director of VES Precision Ltd, said Workflow will dramatically speed up the programming of parts for their aerospace and food industry components, and Waveform has already considerably extended tool life.
EDGECAM SEMINARS HOW TO
Roemheld Managing Director Bill Neal said the growing complexity of components means 5-axis machining is becoming increasingly more popular, and he outlined how to “future-proof” workholding investments for access, component handling, positioning, repeatability and rigidity.ĮDGECAM users said they found the event invaluable in keeping up with EDGECAM’s latest “game-changing” developments. And he highlighted its difference from high feed milling, which he said was a roughing process designed to remove as much material as possible in the shortest time.ĭelegates were also shown how workholding for 5-axis components is “totally different” from standard positioning. He showed how harder carbide tools were used with small arcs of contact, creating small radial cutting depths. Steve Heatherglen, Seco’s Product Manager for Indexable Milling, explained the theory behind high speed machining, outlining machine tool requirements such as NC control, block cycle times, machine rapidity, spindles and run out. Live machining demonstrations were held on a Mori Seiki and AgieCharmilles Mikron showing how Waveform maximises material removal rates while delivering shorter cycle times and prolonging both tool and machine tool life.along with 5-axis machining. He and Pre Sales Manager Lee Richards detailed how Workflow automatically loads a part in the correct manufacturing environment, with datum set, enabling CAD/CAM engineers to apply toolpaths within seconds. How to future-proof their workholding investments.ĮDGECAM engineer Mike O’Neill said Workflow – which was introduced in EDGECAM 2013 R2 – and the Waveform Roughing Strategy launched last year, are the most significant developments in EDGECAM’s history.The essential differences between high speed machining and high feed milling.How EDGECAM’s new Workflow application will help them reduce costs, improve quality and hit shorter lead times.Presentations from EDGECAM, Seco, and workholding specialists Roemheld showed over 130 delegates representing all industry sectors: Manufacturers from around the country attended the seminar, where they learned from Seco’s Business Development Manager – Products, David Magnall, how a dedicated partnership of suppliers forms “the complete solution for the metal cutting industry.” Industry Partnership Forms “Complete Solution”ĮDGECAM celebrated 30 years in the CAD/CAM industry by holding a productivity event at Seco’s new Technology Centre.
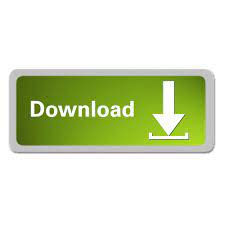